June 1, 2016
From 5 MGD to 1 Billion Gallons per Day
Learn the Secrets Behind 3 of the Biggest Success Stories
in Water Industry Technology Commercialization
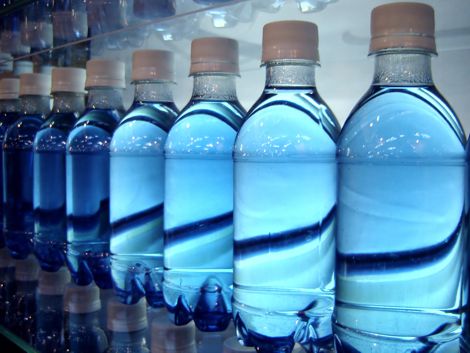
Three of the most spectacular success stories in technology adoption in the water & wastewater industry include:
- the roll out of the Union Carbide (UNOX®) high purity oxygen activated sludge process which treats about 6 billion gallons per day (15% of US wastewater treatment capacity!)
- Cambi's breakthrough in the United States with the adoption of their version thermal hydrolysis process at the 370 MGD Blue Plains Advanced Wastewater Treatment plant and
- Stickney Water Reclamation Facility's (1 billion gallons per day) adoption & recent commissioning of the Ostara phosphorus recovery process.
In each of these cases, massive wastewater facilities have adopted technologies at scales that are as high as over 100 times the size of current pilot or commercial scale installations.
Read on to find out the back story to how these innovative technologies crossed the chasm and got big wins in the water market.
Case Study 1: UNOX® - From 5 MGD Pilots to 720 MGD Full Scale Plants: How Pure Oxygen Claimed 15% of the US Wastewater Market
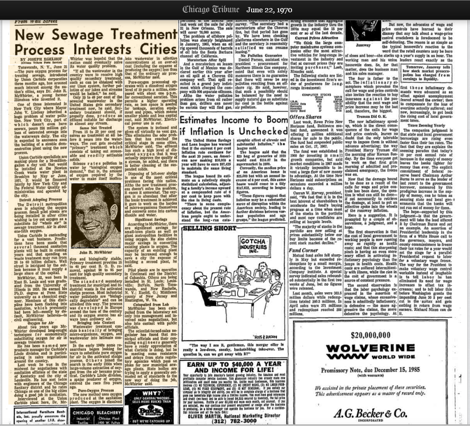
Chicago Tribune Article on the UNOX® process from 1970
Background
This is the oldest of the success stories, and it goes back to the late 1960s. In 1967, a young Engineer at Union Carbide called John McWhirter, came up with a radical new process. At this time only 30% of US cities had secondary wastewater treatment. Many large cities like Detroit, New York and Louisville had no secondary treatment systems, and worried about the footprint that new plants would occupy. McWhirter came up with a simple, but profound technology. Observing that surface aerators provided the oxygen needs of a wastewater plant by spraying water droplets into air - with 21% oxygen, he recognized that if the atmosphere above a wastewater plant could be converted to 100% oxygen, then up to 5 times as much oxygen could be dissolved by the same surface aerator, in the same footprint. Meaning, an activated sludge plant could provide as much as 5 times the treatment in the same space if it had a high purity oxygen headspace instead of air. Fascinating stuff!
This was great news for land challenges cities - but it was a radical idea and it met with some initial resistance. The first pilot scale systems started up in 1967 and by 1970, the City of Detroit had signed up to build a 720 MGD facility.
Solution
The major pushback from utilities and consulting engineers was the lack of experience with the technology and little understanding of the process. In partnership with the EPA and a number of test sites, a set of design and operational guides were published in 1973. The guides provided extensive details on how to size the plant, the impact of pure oxygen on plant operations, clarifier operations, cost, sludge microbiology & solids settling. It essentially provided enough information to let anyone considering the process understand its plant wide impact. The effect was tremendous - adoption shot up. Pure oxygen wastewater plants made up over 20% of all new wastewater plants constructed in the 1970 - 2000 timeframe. Today, pure oxygen based activated sludge systems treat about 6 billion gallons of the 38 billion gallons of municipal wastewater treated daily in the United States. Technology adopters include Detroit (720 MGD), Middlesex (250 MGD), Los Angeles Hyperion (450 MGD) and many others.
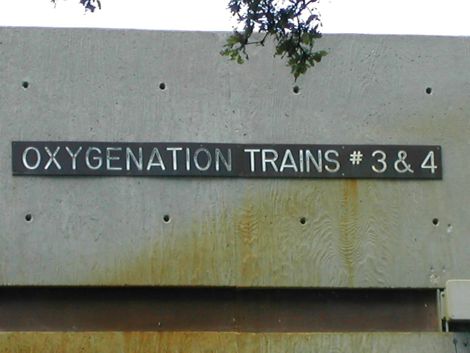
Sign on Treatment Trains at Miami Dade
Oxygen Activated Sludge Treatment Process
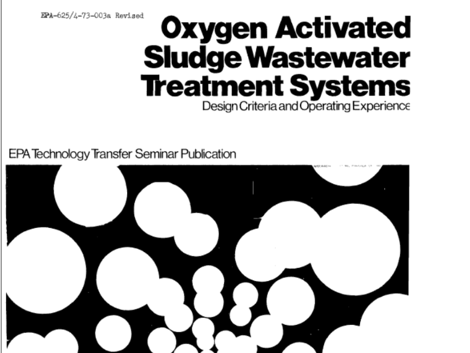
Title page of 1973 Design Guide Released by the EPA
on the Pure Oxygen Activated Sludge Process
Case Study 2: Cambi Successfully Enters US Market with Major Win at 370 MGD District of Columbia, Blue Plains Wastewater Plant
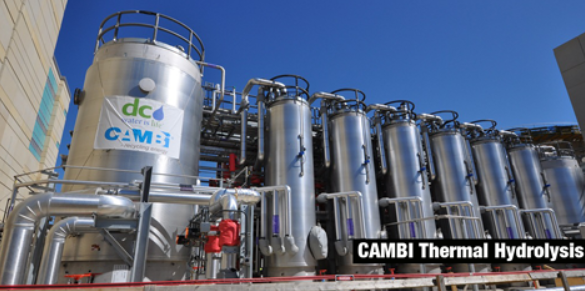
Cambi reactors at DC Water Blue Plains
Wastewater Treatment facility
Background
As interest has increased in recovering more biogas and energy from sludge in anaerobic digesters, a number of innovative technologies have been developed to enhance the digestion process. Only about 30-40% of the energy locked up in a bacterial cell is released in an anaerobic digester. Thermal hydrolysis uses heat and pressure to “burst open” bacterial cells, releasing their energy content for conversion to biogas.
From its origins in 1996, the Cambi thermal hydrolysis process had made some modest progress in Europe, but it made few in roads in the attractive US market. By 2012, its largest sized plants averaged about 30,000 dry tons of solids per year. It turns out that the larger a plant is, the more sludge it has, and therefore, the more biogas and energy it can potentially recover. But, with increasing size comes increasing risk. Operations can get more challenging, higher ammonia levels could potentially inhibit digester performance, and larger recycle streams could potentially compromise effluent quality - jeopardizing the plant's ability to meet its regulatory limits. Unless these questions could be answered, adoption would have to remain slow and tortuous - subject to extended pilots at each plant.
Solution
In 2008, a paper was presented with little fanfare at the Water Environment Federation conference. It was titled “Simulation of Thermal Hydrolysis at the Blue Plains AWT: A New Toolkit Developed for Full-Plant Process Design” - authored by some leading researchers, plant personnel and modelers. It was not the first paper to report on pilot scale thermal hydrolysis studies. But it was one of the first to present a useful modeling framework for handling some of the most vexing questions about the risks involved with the implementation of thermal hydrolysis. Within a couple of years, all the major modeling platforms (Hydromantis and others), had integrated thermal hydrolysis modules into their simulation platforms. This allowed anyone - utilities, consulting engineers, and solutions integrators - reviewing thermal hydrolysis to develop full pant models that would allow then understand the full plant impact of adopting thermal hydrolysis. The results have been impressive. In 2014, Cambi announced that DC Water's massive 370 MGD Blue Plains facility, with annual dry solids of about 140,000 tons per annum would be the first plant in the US to adopt the Cambi process. Since then, the big wins have piled up for Cambi. The company has signed a number of mega deals around the world, a number of which are at the massive scale of the Blue Plains plant.
Case Study 3: Ostara - Doing Big Things with Phosphorus at the 1 Billion Gallons per day Stickney Plant, Chicago
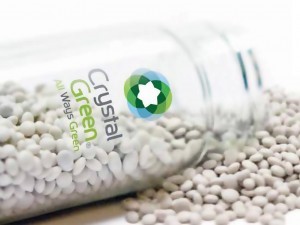
Ostara's Crystal Green Fertilizer
recovered from wastewater
Background
Just last week, the 1 billion gallon per day Stickney Water Reclamation Facility unveiled the world's largest phosphorus recovery plant. The facility is based on Ostara's Pearl® technology and allows the recovery of phosphorus and ammonia as a high grade fertilizer from concentrated waste streams. It was cheering news in an industry that doesn't get a lot of opportunity for celebration.
How did this happen? How did Stickney - arguably the world's largest wastewater plant, come to adopt a technology which had never been installed at a plant larger than 40 million gallons per day prior to the Stickney project?
Solution
Phosphorus recovery like other innovative technologies, can have impacts beyond the point of application of the technology. The process can result in a change in recycled nutrient flows and solid flows. Facilities need to understand the impact of process failures in non-essential processes like nutrient recovery on the plant's ability to meet its regulatory limits. In order to understand the implications of adopting the Ostara process on their facility, Stickney commissioned a process modeling study in 2014 that was carried out using Hydromantis GPS-X™ simulator. The simulator allowed them to develop a plant wide model of the facility. Using this platform, they could run different scenarios and evaluate the impact of different operational regimes on the Phosphorus recovery process, and vice versa. This tool allowed the risks to be better understood. It validated the scale of the opportunity and enabled Stickney to develop a coordinated plan for adopting this innovative technology.
Stickney plant wide model for Struvite recovery developed in Hydromantis' GPS-X
(Source: Koch et al, Phosphorus recovery at the Stickney Water Reclamation Plant. MWEA 2015 Annual Conference)
Dr. Malcolm Fabiyi is President of Hydromantis USA - the leading water & wastewater process modeling & design software firm. He worked as a consultant in McKinsey & Company. Dr Fabiyi was CTO at Environmental Operating Solutions, Inc; and also led the Water & Wastewater Research & Development and Commercialization effort at Praxair, Inc. He holds numerous patents for commercialized water technologies.
He can be reached at info@hydromantis.com